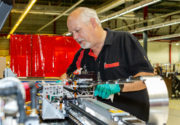
Колонна Автномного Обслуживания (Jishu Hozen) оборудования является локомотивом программы TPM и ставит во главу угла развитие основных производственных компетенций у сотрудников. На плечах современного производства лежит огромная ответсвенность по обеспечению безопасности людей, выпуска качественного продукта, своевременного выпуска готовой продукции с конкурентноспособной ценой, а также защиты окружающей среды от вредного воздействия.
Колонна автономного обслуживания преследует две цели. С точки зрения людей – культивирует развитие знающих операторов в свете их вновь определенной роли. С точки зрения машины – создает упорядоченную рабочую среду, где любое отклонение от нормального состояния определяется с первого взгляда.
Колонна Автономное Обслуживание: основы
Мы живем во времена, когда автоматизация и компьютеризация становиться неотъемлемой частью многих производств. Хотя до сих пор можно встретить различные типы ручной работы на производстве, тренд на автоматизацию очевиден.
Современные индустрии массового производства, работающие по принципам Форда, фокусируются на: 1) стандартизации частей, 2) составе бригады прозводстенной линии и 3) упрощении работы людей. В такой среде работники должны повторно выполнять простую работу без знаний о структуре и функциях машины, на которой они работают, или продукте, который они производят. При таком подходе, от них не ожидается ничего, кроме как выполнять свою рутинную работу. Однако тренд к автоматизации и без человеческого вмешательства, намеченный в промышленности, также требует большого количества ручной работы для обслуживания сенсоров при автоматическом производстве. Также требуется людское внимание при работе с подтеками, разливами, блокировками и другими проблемами в производстве. Лучшие кандидаты на эту роль – те, кто лучше всего знают оборудование.
«Знающий оператор» — не значит, что он может починить оборудование, так же как технический специалист. Скорее здесь важным является возможность оператора определять сигналы будущих проблем. Это значит, что оператор должен чувстовавть что-то неладное во время работы оборудования с ненормальными условиями и предупредить возникновение поломки или дефекта качества.
Почти всем поломкам или дефектам качества предшествуют некоторые сигналы – вибрация, шум, запах, температура. До внедрения TPM, такие сигналы невозмножно детектировать. Но после приведения оборудования в базовое состояния на AM шаге 3, количество поломок в среднем сокращается наполовину. После этого становится возможным определять сигналы.
Следовательно, операторы также ожидают, что дефекты будут устранены на ранних этапах, чтобы избежать потерь. Менеджмент должен обучить операторов отчитываться о ненормальных ситуациях в отдел технического обслуживания или мочь устранить проблему самостоятельно. Для этого, операторы с самых ранних шагов внедрения АМ должны быть обучены базовым рабочим принципам и функциям оборудования и позже обучены на практике на действующем оборудовании.
Это не простая задача и требует определенного количества времени и денег. Тем не менее, это необходимое действие для внедрения TPM.
Оптимальное производство
Если знающего оператора поместить в традиционный грязный завод, где возникает большое количество поломок и малых остановок, он или она не сможет использовать свои возможности. «Оптимальное производство» или другими словами производство, где любой человек может определить отклонения от нормального состояния, будет достигнуто тогда, когда знающие операторы производят продукт на оборудовании с базовым состоянием.
Такой процесс может быть достигнут только когда выполняются два важных условия – соблюдается оптимальный уровень знаний человека и оборудования. В дополнение, уровень знаний человека и состояние оборудования должны соответствовать друг другу. Только при таких обстоятельствах возможно достижение Нуля Инцидентов, Нуля дефектов качества и нуля поломок.
Оптимальные условия оборудования сводятся к установке базового состяния оборудования, при котором оборудование чистое, смазанное и проинспектированное. Помимо этого, установлено визуальное управление, изношенные части заменены и оборудование эксплуатируется правильно.
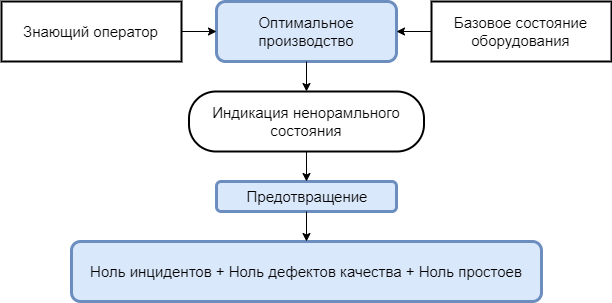
Рост дефектов оборудования
Состояние оборудования, при котором возникают потери можно отнести к дефектам оборудования и разделить на три группы в зависимости от величины и влияния на потери:
Большие дефекты: один дефект на оборудовании, который может быть причиной поломки или операционной остановки.
Средние дефекты: один дефект на оборудовании, который может снизить функциональность оборудования, но не остановить машину.
Малые дефекты: Один дефект, который сам по себе не может вызвать потерю. Только в сочетании с несколькими такими дефектами может привести к потере.
В традиционном понимании менеджмента малые дефекты не ведут к поломкам – например, небольшая грязь, истирание, искажение, игра, ослабление или царапины на оборудовании. Действительно, очень редко один малый дефект может привести к потери. Более того, такие проблемы никогда не решаются при традиционном подходе. С точки зрения TPM, малые дефекты рассмтриваются как возможная причина потерь до тех пор, пока не докажется обратное. Поэтому малые дефекты должны устраняться без обдумавания – влияет он на потери или нет. Если малые дефекты игнорируются, они перерастают в дефекты средней величины, а затем большие дефекты. Этот прогресс изображен на рисунке.
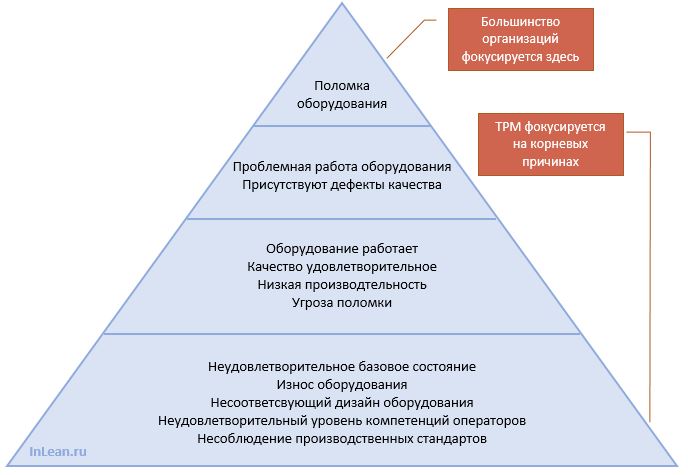
Кроме случаев когда причины четко определены – например, несколько ошибок в расчете прочности, выборе материала, сварке и инсталяции во время дизайна оборудования, произодства и сборки – можно без преувеличения сказать, что почти все поломки возникают по причине средних или малых дефектов. Для достижения Нуля Поломок становится очевидным, что необходимо устранить все дефекты – малые, средние и большие.
Форсированный и естественный износ
Износ запчастей является причиной поломок. Износ можно разделить на две части: естественный износ и форсированный износ.
Со временем, оборудование изнашивается следуя характеристикам износа каждой запчасти, даже если оборудование было правило спроектировано, произведено, установлено, эксплуатировалось и обслуживалось. Этот тип износа относится к натуральному износу.
Форсированный износ возникает, когда оборудование изнашивается быстрее, чем это изначально заложено. Например, некоторые детали оборудования подвержены перегрузкам из-за плохого дизайна, грязи и смазки, или не затянутого крепежа. В более серьезном случае – это ошибки эксплуатации оборудования и восстановления. Фактически, большинство поломок на фабрике случаются из-за форсированного износа.
Приведение оборудования к базовому состянию означает — устранить причины формированного износа. А именно: чистка (убрать все следы глубоко въевшейся грязи, и найти и устранить скрытые дефекты), смазка (предотвратить износ и перегрев, поддерживая смазку в чистоте и пополняя ее), затяжка (предотвращать неисправность и поломки, поддерживая болты и гайти в целостности).
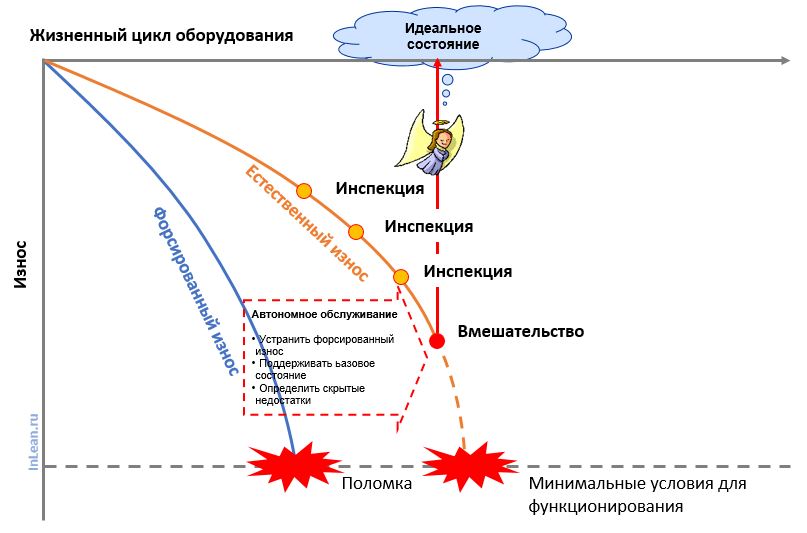
Активность колонны АМ направлена на избежание форcированного износа. Приведение (и поддержание) базового состояния (чистка, смазка, затяжка) является важной частью этого. Фактически, это наиболее значимая часть обслужтвания. В TPM поддержание оборудования в порядке (Housekeeping) означает приведение к базовому состоянию.
Pingback: Что такое Тотальная Производительность оборудования (TPM)? | InLean
Pingback: Базовое состояние оборудования | InLean
Pingback: Шаги Автономного обслуживания и четыре фазы развития | InLean
Pingback: Дерево потерь — Введение, основные понятия — Часть 1 | InLean